CNC零件加工是現(xiàn)代制造業(yè)的核心技術(shù)之一,其流程的規(guī)范化、自動(dòng)化和高精度特性,使其成為復(fù)雜精密零件生產(chǎn)的首選方式,也是工業(yè)智能化升級(jí)的重要基礎(chǔ)。
?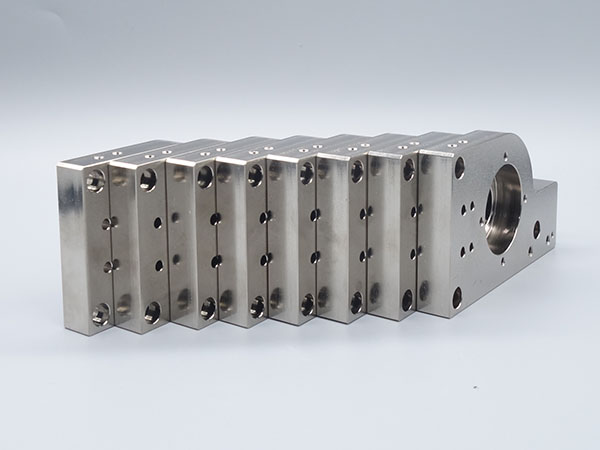
CNC零件加工的工藝流程有哪些方面?1. 前期準(zhǔn)備階段
圖紙分析與工藝規(guī)劃
解讀零件設(shè)計(jì)圖紙(2D 圖紙或 3D 模型,如 CAD 文件),明確尺寸公差、表面粗糙度、材料(如鋁合金、不銹鋼、鈦合金)及性能要求(如硬度、耐腐蝕性)。
制定加工工藝路線:確定加工順序(如 “粗加工→半精加工→精加工”)、選擇機(jī)床和刀具、規(guī)劃裝夾方式(如使用夾具、卡盤、吸盤)。
編程與仿真
根據(jù)工藝路線編寫 CNC 程序:
簡(jiǎn)單零件可手動(dòng)編程(直接編寫 G/M 代碼);
復(fù)雜零件需通過(guò) CAM 軟件(如 UG、Mastercam、SolidWorks CAM)自動(dòng)編程,生成刀具路徑。
程序仿真:通過(guò)軟件模擬加工過(guò)程,檢查是否存在刀具碰撞、過(guò)切(切除過(guò)多材料)、欠切(未切到位)等問題,避免實(shí)際加工時(shí)損壞機(jī)床或工件。
材料與刀具準(zhǔn)備
材料預(yù)處理:根據(jù)零件尺寸裁切毛坯(留 1~5mm 加工余量),去除表面氧化皮或油污;若材料硬度高(如淬火鋼),需預(yù)先退火降低硬度,便于切削。
刀具選擇:根據(jù)材料和加工方式選刀具(如高速鋼刀具用于軟材料,硬質(zhì)合金刀具用于硬材料,陶瓷刀具用于高速切削),并確認(rèn)刀具尺寸(直徑、長(zhǎng)度)與程序匹配。
2. 核心加工階段
裝夾與對(duì)刀
將毛坯固定在機(jī)床工作臺(tái)上(如三爪卡盤夾持軸類零件,虎鉗固定板類零件),確保裝夾牢固(避免加工時(shí)松動(dòng)導(dǎo)致尺寸偏差),同時(shí)減少工件變形。
對(duì)刀:通過(guò)對(duì)刀儀或手動(dòng)對(duì)刀,確定刀具與工件的相對(duì)位置(設(shè)定工件坐標(biāo)系原點(diǎn)),將刀具長(zhǎng)度補(bǔ)償、半徑補(bǔ)償參數(shù)輸入機(jī)床系統(tǒng),保證加工尺寸精度。
切削加工(按工序執(zhí)行)
粗加工:快速去除大部分余量,優(yōu)先保證效率,選用大進(jìn)給量、低轉(zhuǎn)速(如銑削時(shí)進(jìn)給速度 500~1000mm/min,轉(zhuǎn)速 1000~3000r/min),預(yù)留 0.5~2mm 精加工余量。
半精加工:修正粗加工后的形狀誤差,接近零件最終尺寸,為精加工做準(zhǔn)備。
精加工:以高精度、高光潔度為目標(biāo),選用小進(jìn)給量、高轉(zhuǎn)速(如銑削轉(zhuǎn)速 5000~20000r/min),確保尺寸公差和表面粗糙度達(dá)標(biāo)(如 Ra1.6μm 以下)。
中途檢測(cè)
關(guān)鍵工序后通過(guò)量具(如游標(biāo)卡尺、千分尺、百分表)或三坐標(biāo)測(cè)量?jī)x(CMM)檢測(cè)尺寸,若超差及時(shí)調(diào)整程序參數(shù)(如進(jìn)給量、切削深度)。
3. 后續(xù)處理階段
去毛刺與清洗
去除加工后零件邊緣的毛刺(可通過(guò)手工銼削、砂帶打磨或?qū)S萌ッ虣C(jī)),避免裝配時(shí)劃傷或影響精度。
清洗零件表面的切削液、鐵屑和油污(用超聲波清洗或清洗劑擦拭)。
表面處理(可選)
根據(jù)需求進(jìn)行表面處理,如:
金屬零件:電鍍(鍍鉻、鍍鋅防銹)、陽(yáng)極氧化(鋁合金增強(qiáng)耐磨性)、噴砂(增加表面粗糙度);
塑料零件:拋光(提升光潔度)、噴漆(美觀 + 防護(hù))。
最終檢驗(yàn)與入庫(kù)
按圖紙要求全面檢測(cè)零件尺寸、形位公差(如平行度、垂直度)、表面質(zhì)量,合格后標(biāo)識(shí)入庫(kù)。